Implementation:
To tackle the unstable operational challenges, ME Elecmetal replaced the SMX lifters with the ME PolyLight solution. Featuring a plate with rolled steel inserts paired with a cast lifter section, the design provided enhanced impact resistance while maintaining the original mill volume — avoiding the need for thicker, heavier liners.
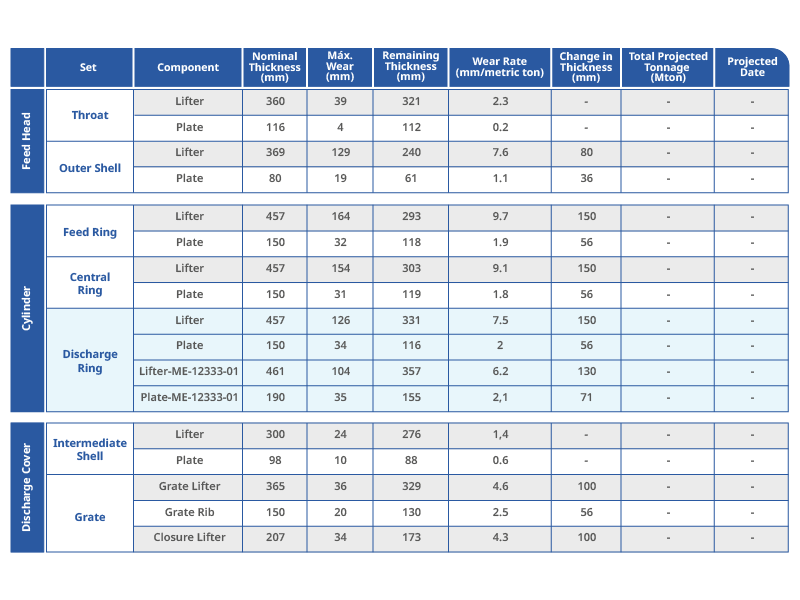
Test Campaign Highlights:
- Processed 16.89 million tons over 199 days.
- Wear patterns were consistent with historical trends.
- Initial assessment based on grates installed on 08-23-2023.
Results:
- Achieved a 17% reduction in wear rates.
- No insert detachment or fractures were observed in cast elements.
- Successfully absorbed operational variability without compromising liner integrity or requiring unplanned maintenance.
- Demonstrated that enhanced durability can be achieved without reducing internal mill volume.
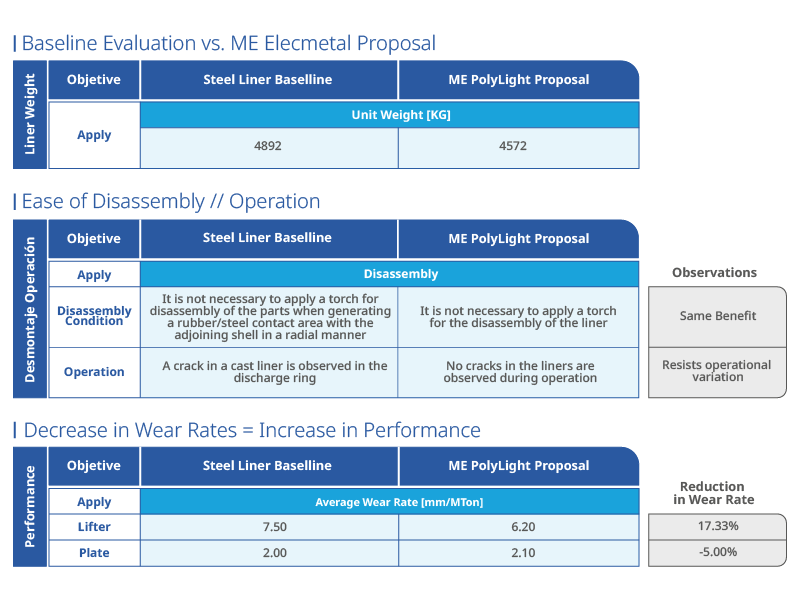
The ME PolyLight solution validated ME Elecmetal’s innovative approach to liner design — delivering superior reliability, operational flexibility, and sustainability benefits while driving down maintenance costs and downtime.